Introduction to Hazardous Locations
Before an electrician or technician performs maintenance, testing, troubleshooting, or repairs on any electrical device in a location where flammable gasses or vapors could release into the atmosphere, it is important to establish if the location in question is a hazardous location. A hazardous location is a location that contains flammable gases, vapors, or dust. One example of a hazardous location would be a gas station. It is important to understand if a piece of equipment (like a pump, switch, sensor, etc.) is located in a hazardous location, so that appropriate safety procedures can be used.
It is very important to understand what hazardous locations are, because equipment in hazardous locations is very carefully designed and constructed in order to ensure that it does not spark, and therefore ignite gases or vapors coming from the combustible stuff in the area. If it did spark, it could cause an explosion.
Hazardous locations are divided into classes, divisions, and groups, which indicates how dangerous the location is based on the materials present. One of these standardized designations is Class 1 Division 2 .
Class 1 Division 2 means that explosive materials may be present in the location only occasionally, under abnormal conditions. Although it is not as bad as a Class 1 Division 1 location, a Class 1 Division 2 location can still be quite dangerous. While it may sound unintuitive, Class 1 Division 2 is actually a more dangerous designation than Class 1 Division 1. This is because equipment in a Class 1 Division 1 location is designed to cut off power immediately in the presence of a Class 1 Division 1 level dangerous substance, whereas equipment at a Class 1 Division 2 location has a delay to cut off power, since dangerous substances won’t be present most of the time. So in a Class 1 Division 2 area, the risk of equipment malfunction is present whenever an explosive material is present, but not present for all of the time.
It is very important for electricians and technicians to understand whether or not a location is a Class 1 Division 2 location. Although they may be called in to do routine maintenance or troubleshooting in a Class 1 Division 2 area, there may be a dangerous substance present without them knowing it. Simple wires, terminals, and buttons could potentially cause a spark that could result in injury or worse.
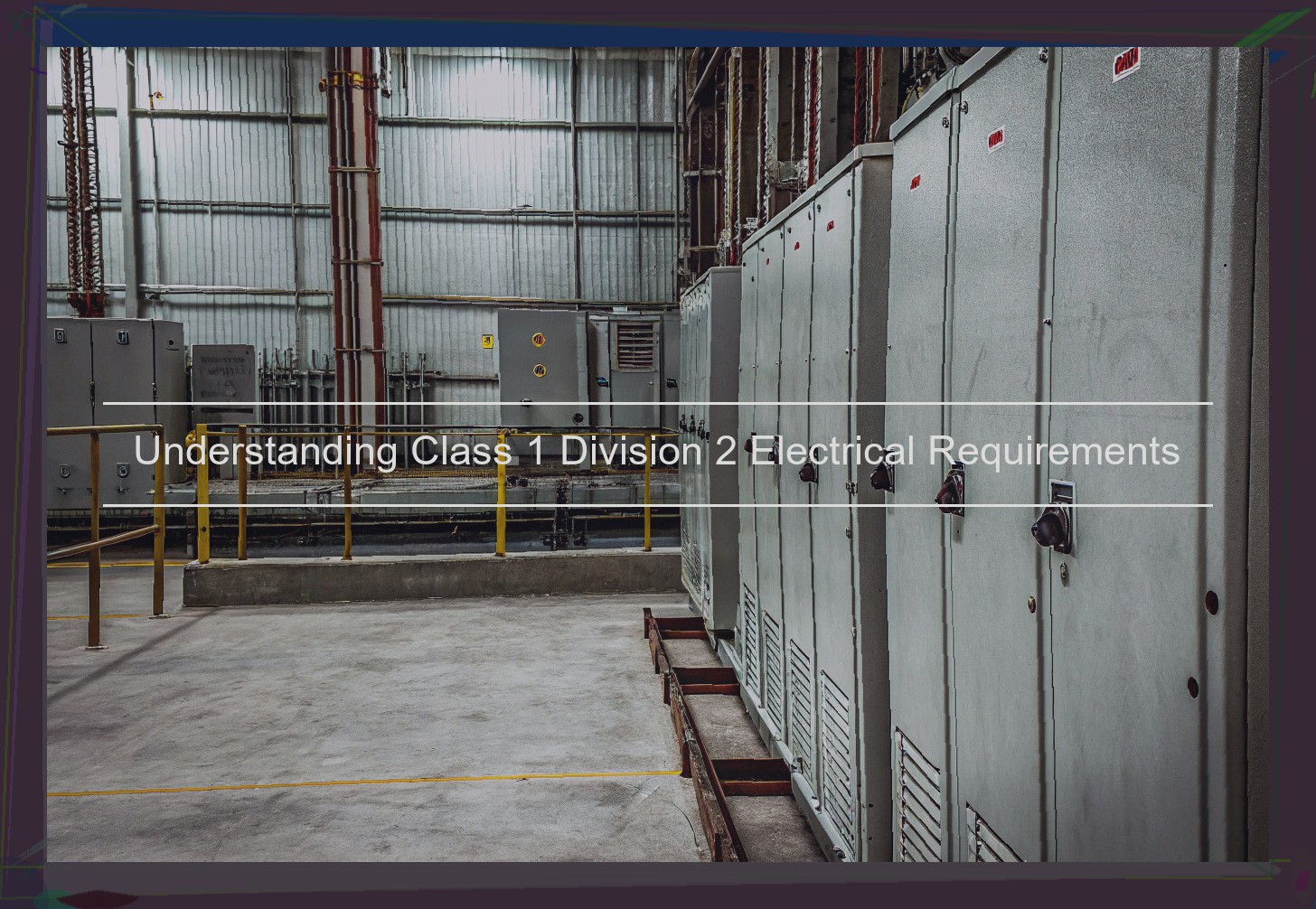
Defining Class 1 Division 2 Areas
Class 1 Division 2 locations are defined as those areas "where flammable vapors or gases may exist under abnormal conditions such as an accidental break or leakage of a gas pipe or in abnormal operations of heating equipment or in a gas refueling area."
Flammable vapors or gases may be present in these areas under normal conditions and may include materials such as acetylene, hydrogen, ethylether, ammonia, butane, propane and gasoline vapor. The only difference between Class 1 Division 2 areas and their Division 1 counterparts is that Division 2 may have an ignition source under abnormal operational situations such as a pipe leak or other ruptured container. Essentially, Division 2 areas are exposed to occasional or intermittent exposure to ignitable concentrations of flammable gases or vapors, while Division 1 areas are subject to constant or continuously present conditions. These environments differ from Class 2 and Class 3 areas in that materials that may be present are conductive, rather than non-conductive. They are also not be capable of supporting life and, in general, are not explosive mixtures.
Electrical Equipment Requirements
To comply with National Electrical Code (NEC) 505 and OSHA 1910.307, the electrical equipment in the area must be evaluated and certified for use in Class 1 Division 2. In addition to the general requirements for explosion proofing that exist, each electronic device must meet the standards of the Class 1 Division 2 environment. For example under Class 1 Division 2, a manufacturer may install an electronic relay control. However, the electrical signal that operates that relay and the circuitry that connects the relay to the electrical controls must be appropriate for use in that environment. If the device in question is accepted by Underwriters Laboratories (UL), it provides a level of assurance that the device complies with the standards for Class 1 Division 2 use. However, this does not mean that all UL devices are suitable for Class 1 Division 2 environments. The proper UL certification will read CL I, Div 2 Div1 – UL514A (or equivalent). This lists the equipment as suitable for Class 1 Division 1 and division 2, indicating that the device has been constructed and tested for use in Class 1 Division 2 locations. The use of devices marked Cl I Div II div 2 – UL 514A (or an equivalent designation) evidences that the manufacturer of the device subject to Class 1 Division 2 testing accepts responsibility for their statement. The UL certification is almost always more rigorous than the associated IEC, CSA or other certification. However, the basic IEC and similar standards can be used as a guideline to determine if the device is acceptable for use.
Installation Guidelines and Best Practices
A variety of installation guidelines and best practices apply to electrical installations in Class 1 Division 2 areas. These electrical requirements are designed to mitigate the risk of ignition of combustible gases and vapors in such hazardous locations.
In Class 1 Division 2 areas, electrical equipment may be installed with fewer restrictions than in Class 1 Division 1 areas, where equipment is required to meet higher standards. In Division 1, electrical equipment is subject to restrictions that generally apply to Class 1 environments, which means many of the Division 1 guidelines are also applicable to Division 2 areas.
Electrical equipment used for installation in Class 1 Division 2 areas must be approved per the subparts of Part 18 that contain diagnostic standards. Diagnostic standards offer end users a standardized method of ensuring that electrical installation meets design and/or approval evaluation standards set out in the National Electrical Code® (NEC).
In Class 1 Division 2 areas where hazardous materials or substances may occasionally be present, all electrical equipment must meet the requirements of 30 CFR § 18.73, which outlines general requirements for electrical equipment design, manufacturing, and installation for such locations.
Electrical installation design in Class 1 Division 2 areas must a review of the design and construction of the building facility and the potential for the presence of liquids or gases designated as flammable divisions under the National Fire Protection Act (NFPA) in the areas planned to house electrical equipment.
Compliance and Regulations
In the U.S., compliance with National Fire Protection Association (NFPA) standards has become one of the key components of the certification process. Compliance means more than just having the right electrical and mechanical characteristics, it means having adequate safety margins under all conditions of normal and emergency operation. Compliance is assured by selecting the correct components for the equipment to be used in the particular application, and by following the correct installation and testing procedures. The National Electric Code (NEC), published by the NFPA, covers the compatibility requirements for electrical components in terms of general safety, reliability and efficiency. Compliance with NEC is essential when dealing with Class 1 Division 2 applications. The NEC is designed to reduce the possibility of accidents and to encourage consistent safety practices in every area of electrical engineering. Adherence to code allows manufacturers and employers to defend their practices and may be considered a defence in law. One of the key areas dealt with by the NEC is that of hazardous locations. Methods such as purging and pressuring are covered in the regulations. There are essentially four methods, as defined by NFPA 496. Purging: this method involves filling the enclosure with a suitable gas, or inert liquid, for a prescribed period of time with a designated flow rate in order to remove any potentially hazardous gas. Pressurization: a method of ensuring that the concentration of the gas outside the enclosure only comes into contact with a small volume of the enclosure gases . These gases are ensured to be below the explosive concentration. Purging and Pressuring: this is a combination of both of the methods mentioned above. Oil immersion: where the gas outside the enclosure only comes into contact with a small volume of the gases inside the shell. The gases inside the enclosure must only be able to combust or explode outside the enclosure when the temperature of the gas exceeds the ignition temperature of the gas outside the enclosure. In the UK, compliance with the Institute of Electrical Engineers (IEE) Code of Practice for Electrical Equipment for Explosive Atmosphere (Protective Systems) is mandatory. The IEE covers all aspects from product design to maintenance. Compliance is achieved when products meet the industrial standard specifications set by the IEE. The equipment being used in this application must adhere to common industrial standards such as the ATEX directive, the IEC code, as well as IEC 60070-15. As with compliance in the U.S., all aspects of the equipment must be accounted for -including installation and maintenance. Its necessary that Class 1 Division 2 products are regularly maintained, and most manufacturers insist on a thorough inspection after the equipment has been in operation for three to six months. Ideally, inspections should be performed by a qualified technician. This includes a review of the mechanical integrity of the enclosure, grounding, etc. It’s recommended that inspections are scheduled on a regular basis; because, as we all know, if we schedule an activity for the future, there’s a much greater degree of compliance than if we leave it to the convenience of the future.
Emerging Technologies in Innovation
Emerging technologies and innovations continue to play a significant role in the electrical and industrial sectors. With the rapid pace of technological change, understanding the impact on compliance with Class 1 Division 2 requirements is more critical than before.
The first area of innovation has been the move away from the use of un-dotted lead wires in Class 1 Division 2 circuits. Historically, the diodes and resistors would be placed in a circuit with the long former length lead connected to the circuit board. This results in the lead extending outside the enclosure into the Class 1 Division 2 area. Currently many manufacturers have developed alternative methods to ensure the circuit protection without going outside the enclosure. These advantages include:
In addition to the previously mentioned changes, when considering component changes or upgrades, many manufacturers are designing new printed circuit board (PCB) assemblies as a single large component rather than several components tacted together. The result is a smaller footprint that has fewer parts that could potentially have an increased risk of overheating, arcing, or other forms of ignition. This also reduces the chances of potential combustibles coming in contact with electrical components that may create an ignition source.
The last notable area of innovation has been the development of monitoring systems that provide potential failure indications before they occur. Some no motion switches detect mechanical failures such as worn out bearings or loose belts before a catastrophic failure could occur. This allows systems to be proactively repaired which greatly reduces the possibility of an ignition source.
New technologies and innovations are presenting very interesting opportunities, as well as challenges. There is significant momentum towards increasing the use of digital communication particularly in industrial settings where the industry is looking to increase productivity, efficiencies and performance. We will need to develop new approaches to Industry 4.0 and the Internet of Things (IoT) while maintaining safe operation in potentially explosive environments.
Conclusion and Safety Tips
Maintenance and ongoing education is always important when it comes to electrical safety. This is especially true in Class 1 Division 2 areas. Even with the proper equipment, employees must be familiar with safety guidelines and step-by-step procedures for operating in a hazardous area. Some of the safety tips that should be taken into consideration at all times are: Employees who are able to identify any electrical hazards must report them immediately so that the condition can be corrected or brought to the attention of someone qualified to correct it. If you can see it, you can prevent it from becoming a problem. Testing and maintenance are vital to the proper function of all electrical systems , but especially those in hazardous environments. Some top maintenance tips to remember include: Full knowledge of the electrical equipment and systems in the environment is the best way to prevent accidents or injuries. With this understanding comes increased awareness and confidence on the job, which has prevention benefits in and of itself. Ensuring that there are adequate safety procedures and personnel in place creates a general sense of safety and security. When you take the time to inspect, test, and maintain your equipment and hire properly trained staff, you send a strong message to your employees that their safety is a priority. Education and communication can go a long way in promoting safety in your Class 1 Division 2 electrical environments. When in doubt, take a proactive approach and increase your knowledge. Knowing the risks can help you maintain a high standard of safety while creating a well-informed workforce.